The normal use of CNC lathes must meet the following conditions: the power supply voltage fluctuation at the location of the machine tool is small, the ambient temperature is less than 30 degrees Celsius, and the relative temperature is less than 80%.
Environmental requirements
The location of the machine tool should be far away from the vibration source, direct sunlight and thermal radiation, and humidity and airflow should be avoided. If there is a vibration source near the machine tool, an anti-vibration trench should be set around the machine tool. Otherwise, it will directly affect the machining accuracy and stability of the machine tool, and cause poor contact of electronic components, failures, and affect the reliability of the machine tool.
Power requirements
Generally, CNC lathes are installed in machining workshops, not only because of the large environmental temperature changes and poor use conditions, but also various electromechanical equipment, resulting in large fluctuations in the power grid. Therefore, the location where the CNC lathe is installed requires strict control of the power supply voltage. The power supply voltage fluctuation must be within the allowable range and remain relatively stable. Otherwise it will affect the normal operation of the CNC system.
Temperature condition
The ambient temperature of the CNC lathe is less than 30 degrees Celsius, and the relative temperature is less than 80%. Generally speaking, an exhaust fan or air cooler is arranged inside the numerical control electric control box to keep the electronic components, especially the central processing unit's working temperature constant or the temperature difference changes very small. Excessive temperature and humidity will reduce the life of control system components and cause more failures. The increase in temperature and humidity and the increase in dust will cause adhesion on the integrated circuit board and cause short circuits.
Standard use of machine tools
When using the machine tool, the user is not allowed to change the parameters set by the manufacturer in the control system at will. The setting of these parameters is directly related to the dynamic characteristics of each part of the machine tool. Only the value of the gap compensation parameter can be adjusted according to the actual situation.
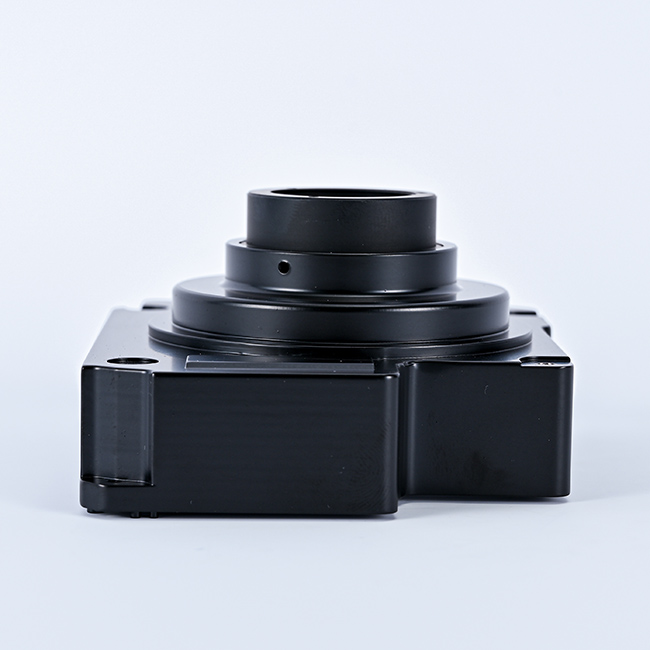